Summary Airbus A380's production delays affected the wiring, with over 100,000 wires and 40,000 connectors redone. Assembly process challenges stemmed from diverse work cultures, software incompatibilities, and multiple location sub-assemblies. Despite production ending, A380s remain beloved, flown nearly a million flights, carrying 300 million passengers.
The Airbus A380 is the world’s largest passenger aircraft. After over a decade of research and development, Airbus launched the double-decker jet in December 2000. The maiden flight took place from Toulouse, France, five years later, on April 27, 2005.
The initial production that was supposed to start in 2004 was delayed by over two years due to difficulties in electrical wiring. Airbus delivered its first aircraft to Singapore Airlines on October 15, 2007. The superjumbo entered service with the airlines on October 25, 2007.
The wiring problem During the summer of 2004, large sections of fuselage arrived in Toulouse from various A380 production sites as part of the final assembly process. A team of 200 German engineers and mechanics arrived in Toulouse to lay hundreds of kilometers of electrical wiring onboard the first plane. An Airbus A380 has over 330 miles (530 km) of electrical wiring.
The Airbus A380's cockpit and cabin have large commonalities, in terms of systems, controls, and processes. As such, all wires connecting the systems must be consistent and show work across the entire cabin and its systems. According to Airbus , Airbus commonality extends from the flight deck into the passenger cabin as well, with a maximum use of similar systems, control panels and procedures across the aircraft families.
As a result, cabin personnel benefit from familiarity of aspects on different Airbus aircraft, while aircraft maintenance is streamlined by the high interchangeability of systems and parts." The Airbus A380 has five sets of landing gear and 22 wheels. Various groups spent weeks threading the wires into thousands of veins for installation.
As the group began to lay the cables along the walls and floor panels of the airframe, they realized that the cables were too short. According to an Airbus employee, “The wiring wasn’t following the expected routing through the fuselage, so when we got to the end, they weren’t long enough to meet up with the connectors on the next section” – Final Assembly Mechanic, Airbus. Airbus soon realized that the design calculations for the wiring needed to be corrected.
Nearly 100,000 wires and 40,000 connectors were affected, and the entire work had to be redone from the design stage. Get the latest aviation news straight to your inbox: Sign up for our newsletters today. The Airbus A380 has one of the most customisable cabins in commercial aircraft given its impressive footprint across two decks.
While British Airways puts first class on the main deck to avail of the wider cabin, Emirates and Etihad put the premium cabins upstairs to make use of the space at the front of the cabin for showers and The Residence. Personally, I think British Airways has one of the best configurations, albeit with an outdated cabin. For me, the highlight of the British Airways A380 is when you are an economy passenger.
There is a small economy cabin at the rear of the upper deck with a 2-4-2 config compared to 3-4-3 on the main deck. As the cabin isn't as long it feels more intimate. What is your favourite A380 cabin? Let us know below! (Photo: Tom Boon - Simple Flying) The root cause Assembly process across multiple locations Use of different software packages Limited compatibility across systems Diverse work cultures impacting the shared design Various sections of the Airbus aircraft are sub-assembled at different locations across Europe.
Large sections come together at one of four final assembly factories, including one in Toulouse, France. Since the 1990s, Airbus engineers in France have used CATIA and CIRCE as their two software packages for three-dimensional computer modeling. At the onset of the A380 program, the program head persuaded the German and Spanish design teams to adapt to the French software for the A380.
The German engineers preferred to use Computervision, a design software developed by a US company. While the software was approved practice for years, it only produced two-dimensional designs. German engineers thought that French practices were being imposed on them.
Moreover, switching to a new software package did not convince the German Management. According to a consultant from a Hamburg design shop, “Changing over to new software is costly and time-consuming. Nobody in upper management wanted to get their hands dirty” – Consultant, Airbus Hamburg.
The management at Toulouse blamed its German counterpart for miscalculating electrical wiring. In reality, the failure to transfer the design files between various Airbus production facilities led to discrepancies in electrical wires. A month into the maiden flight, Airbus made its first public announcement of the production delay of six months.
A year later, in 2006, Airbus announced a second delay of six to seven months. With an eventual delay of over two years, Airbus incurred an initial loss of nearly $7 billion (€5.5 billion).
Impressive statistics Completed nearly a million flights Carried more than 300 million passengers since 2007 Planned to fly well into 2030s and beyond. Today, while A380 production has ended, it remains one of the favorites for pilots and passengers. The iconic A380 has flown nearly a million flights, carrying more than 300 million passengers since its entry into service.
Airbus states that the A380 will keep flying for decades to come. The manufacturer will fully support the operators and their fleets. From the airline's unconventional concept to the latest progress in acquiring A380s, there's a lot to learn about Global Airlines.
.
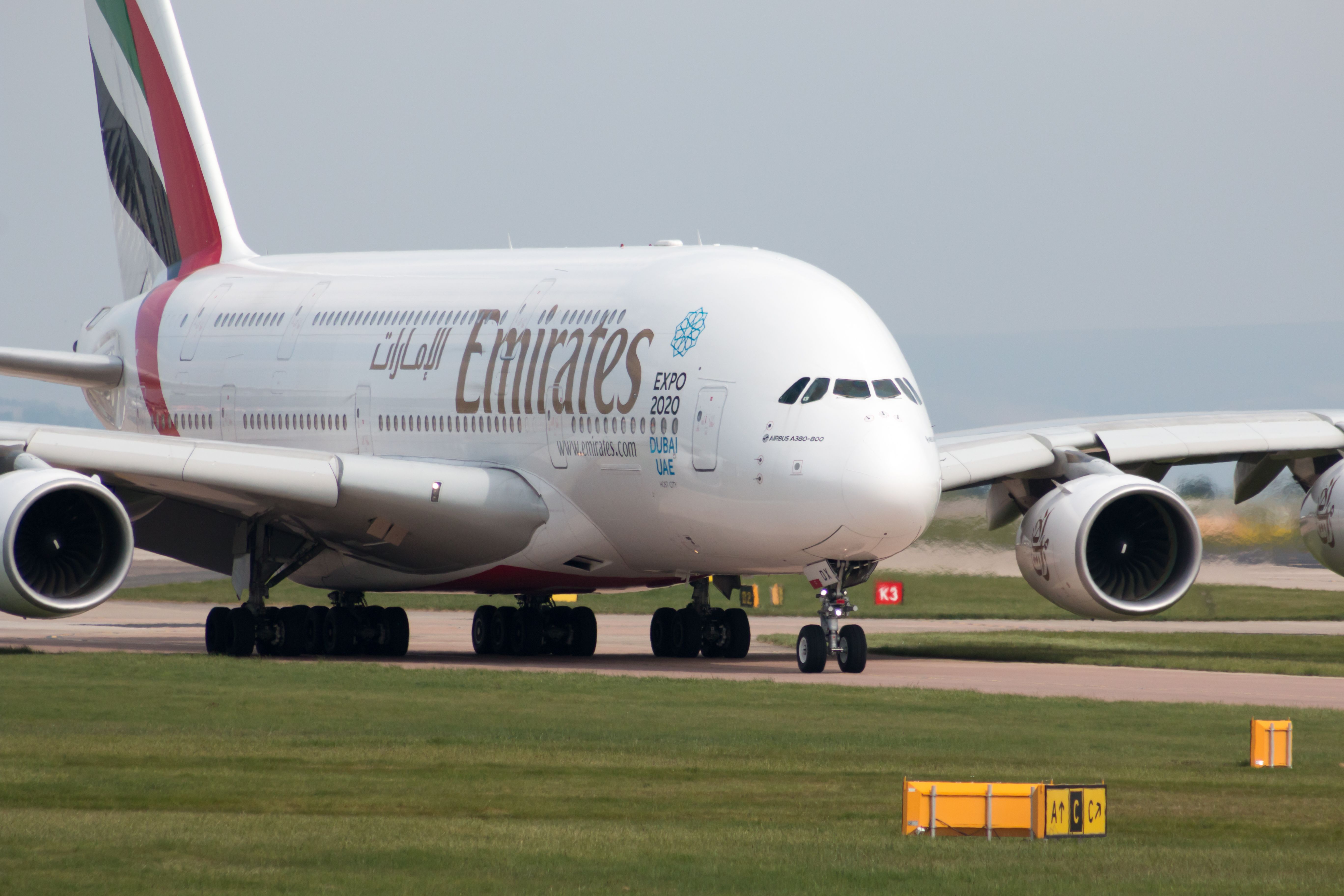