The Supreme Court’s ruling promised equality, but in practice, have the companies caught on? In Pakistan, the plight of the workforce often escapes the scrutiny of its corporate titans. Labour laws, especially those concerning the rights of contracted workers, have long been an overlooked aspect of the country’s economic landscape. But in December 2017, the Supreme Court of Pakistan delivered a landmark ruling that was set to redefine the rules of the game.
The verdict declared that contracted employees should be afforded the same rights as permanent employees—a move that, on paper, was revolutionary. Yet, the question remains: do companies really see it that way? The court’s decision was expected to send shockwaves through the employment market. It broadened the definitions of contract and third-party employment, and mandated that many of these workers be regularized, even applying this retrospectively.
The ruling elevated the status of contracted workers, positioning their rights as a fundamental element of citizenship, not just a legislative afterthought. Before this ruling, the distinction between permanent and contracted workers was stark. Permanent employees enjoyed the security of better wages, retirement benefits, paid overtime, and the luxury of leaves and vacations.
Contracted workers, however, were seen as a disposable extension of the workforce—hired through third parties, they were let go as soon as the seasonal demand subsided. This system offered companies the flexibility to scale their workforce up or down without the financial burden of long-term benefits. The cost savings were so substantial that many factory owners developed elaborate schemes to keep the majority of their workforce on a contractual basis, even resorting to practices like hiring workers for just 89 days to avoid the 90-day threshold that would require them to be classified as permanent.
The Supreme Court’s ruling aimed to curb these exploitative practices. The intent was clear: it was no longer viable for seths to follow the letter of the law while ignoring its spirit. But what has this meant for companies in the short term? One immediate impact was the anticipated rise in salary expenses, as companies were now required to treat all employees equally.
This raised questions about which sectors would feel the squeeze the most. The auto industry, heavily reliant on contracted labour to meet fluctuating demand, stood out as particularly vulnerable. Why contractual labour exists Contractual labor has been a cornerstone of Pakistan’s corporate strategy, particularly within industries that demand flexibility and cost efficiency.
The original system, which distinguished between permanent and contracted workers, provided companies with significant advantages that were too enticing to ignore. Understanding why contractual labor became so prevalent in the first place requires an exploration of the economic and operational incentives that drove this trend. At its core, the use of contractual labor was a response to the need for adaptability in production.
Companies, especially those in sectors like automotive manufacturing, faced seasonal fluctuations in demand. Permanent employees, who were entitled to a range of benefits such as incremental wages, retirement benefits, and paid leave, represented a fixed cost that could become burdensome during periods of low demand. In addition, they are harder to fire.
In contrast, contracted workers could be hired for short stints to meet temporary production spikes and then easily let go once the demand subsided. This flexibility allowed companies to maintain a lean workforce while scaling up quickly when necessary. Another significant factor was the cost savings associated with contractual labor.
Permanent employees were costly, not only due to their higher wages but also because of the additional benefits and protections they were entitled to. Companies that relied heavily on permanent staff had to account for these ongoing expenses, which could erode profit margins. In contrast, contracted workers were typically paid less and did not receive the same benefits, making them a more economical choice for companies looking to maximize profitability.
As companies recognized the financial advantages, many devised strategies to keep the majority of their workforce on a contractual basis. Some even resorted to hiring workers for just 89 days, cleverly circumventing labor laws that would have required them to classify these workers as permanent if they worked 90 days or more. This practice allowed companies to exploit the benefits of a flexible, low-cost workforce without the financial commitments associated with permanent employment.
Thus, contractual labor was initially embraced for its ability to provide companies with the dual benefits of operational flexibility and cost efficiency. However, this system also perpetuated inequality within the workforce, as contracted workers remained vulnerable to exploitation, with fewer rights and protections compared to their permanent counterparts. The auto industry under scrutiny In Pakistan’s auto sector, the gleaming new cars rolling off assembly lines tell only part of the story.
Behind the scenes, a vast army of blue-collar workers powers this industry, many of whom are contracted through third-party agencies. Estimates suggest that around 1.8 million people are directly employed in car assembly, with this number swelling to 3.
5 million when considering ancillary production. In terms of the profile of the labour, the blue-collar workers in the industry typically have 10 to 14 years of schooling and recruitment is done through apprenticeships. These apprenticeships are done at a monthly stipend less than the minimum wage and are covered by the Apprenticeship Ordinance of 1962.
Once these workers are made permanent, their wages can vary between Rs 16,000 to Rs 45,000. When the same figures are seen for contracted workforce, it is evident that they get lower wages and no benefits. The auto sector’s reliance on contracted labour is well-documented.
Typically, 20% of the workforce in this industry is hired on a contractual basis, with the remaining 80% being permanent employees. These contracted workers often receive lower wages and lack the benefits—like retirement benefits, overtime pay, and insurance—that their permanent counterparts take for granted. In recent years, the sector has faced significant challenges, particularly after the government imposed a ban on imports in 2022 to conserve foreign exchange reserves.
This, coupled with a steep depreciation of the rupee and soaring inflation, pushed up production costs, driving car prices higher and dampening demand. As a result, companies were forced to shutter production lines for weeks, even months. The big players: Pak Suzuki and Honda Atlas Cars To assess the impact of the Supreme Court’s ruling on the auto sector, let us examine two of the industry’s heavyweights: Pak Suzuki and Honda Atlas Cars.
Both companies have disclosed their use of contracted labour, making them prime candidates for analysis. In 2017 and 2018, Pak Suzuki’s production capacity stood at 150,000 cars and 44,000 motorcycles annually. As production ramped up, so too did the number of employees, rising from 1,345 in 2017 to 2,024 in 2018.
However, the company did not specify how many of these workers were permanent versus contracted. Financial data, though, offers some clues. In 2017, outsourced labour costs were Rs958 million, increasing to Rs1,060 million in 2018.
Meanwhile, salaries and benefits for permanent employees grew from Rs1.3 billion to Rs1.8 billion.
These figures suggest that the reliance on contracted labour as a percentage of total labour costs actually decreased slightly after the Supreme Court’s ruling. Fast forward to 2023, and Pak Suzuki’s situation had deteriorated significantly. Production fell by 68% for cars and 64% for motorcycles compared to 2018 levels, largely due to plant shutdowns and dwindling demand.
Despite this, the company maintained a relatively stable headcount, suggesting that it leaned more on its permanent workforce during tough times. Outsourced labour costs dropped to Rs758 million in 2023, while salaries and wages for permanent employees rose to Rs2.9 billion, indicating that contracted workers bore the brunt of the cutbacks.
Honda Atlas Cars presents a similar story. In 2017, the company produced 34,500 cars, ramping up to over 50,000 in 2018. Employee numbers rose accordingly, but like Pak Suzuki, Honda did not distinguish between permanent and contracted workers in its disclosures.
Labour-related expenses increased from Rs1 billion in 2017 to Rs1.3 billion in 2018. By 2023, however, the company had slashed its workforce by a third, in line with a significant drop in production, yet overall wage expenses remained steady—a strong indicator that contracted workers were the first to be let go.
The verdict: contracted labour still at risk The data from Pak Suzuki and Honda Cars suggests that despite the Supreme Court’s efforts to level the playing field, contracted labour remains a vulnerable segment of the workforce. When economic conditions sour, these workers are often the first to face the axe, while permanent employees enjoy greater job security. The ruling may have ensured equal treatment on paper, but in practice, contracted workers continue to serve as the industry’s first line of defense against economic downturns.
As Pakistan’s auto sector grapples with an uncertain future, the fate of its contracted workers hangs in the balance. While the Supreme Court ruling was a step towards greater equality, its impact on the ground remains uneven. For now, the seths may have adjusted their strategies, but the fundamental disparities between permanent and contracted workers persist.
In an industry where flexibility and cost savings often trump workers’ rights, the road to true equality may still be a long one. Save my name, email, and website in this browser for the next time I comment. Δ document.
getElementById( "ak_js_1" ).setAttribute( "value", ( new Date() ).getTime() );.
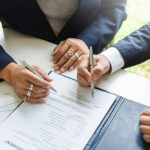