Summary Extensive use of composite materials contributes to the A350's structural strength and fuel efficiency. Airbus utilizes composite materials like CFRP to achieve needed rigidity and reduce aircraft weight. The lightweight A350 structure results in lower fuel burn, reduced maintenance needs, and an extended aircraft lifespan.
The wing performance of the Airbus A350 makes the aircraft unique in terms of its flight performance, fuel efficiency, and passenger comfort. The wing area, aspect ratio, and sweep angle significantly contribute to the A350's outstanding fuel efficiency. Alongside the design, the aircraft’s empty weight largely determines the overall performance of the aircraft.
The use of lightweight composite materials, particularly on critical structural components, made the A350 a game-changer in its class. The sizable iterations Airbus performed before finalizing the A350 design platform have largely contributed to the success of the airliner. The use of composite materials Composite materials on more than 50% of the aircraft structure Carbon Fiber Reinforced Plastic (CFRP) Lightweight High strength Less prone to fatigue and degradation Airbus first used composite materials on the vertical stabilizer of the A300 aircraft more than 50 years ago .
The most modern Airbus widebody, the A350-XWB, comprises composites on more than 50% of its structure. A composite material, as the name suggests, is a unique combination of two or more materials whose characteristics, when combined, exhibit extraordinary physical and chemical properties. One such composite is carbon fiber-reinforced plastic (CFRP), in which microscopic carbon fibers are attached to a plastic resin.
Individually, the carbon fibers or plastic resin could not provide the mechanical and thermal properties required for an aircraft structure. Carbon fiber aircraft like the 787 and A350 reduce jet lag by increasing cabin pressure and improving humidity. However, by precisely combining the two, the strength of the composite surpasses that of many conventional metals, including aluminum and iron.
Moreover, the composite becomes much lighter than Aluminum, with much increased resistance to corrosion. According to Airbus , "From nose to tail, Airbus utilizes advanced composites in its jetliner product line that have been at the forefront of materials science. One particular standout material is carbon-fibre reinforced plastic, or CFRP.
Composed of carbon fibres locked into place with a plastic resin, CFRP offers a better strength-to-weight ratio than metals and has less sensitivity to fatigue and corrosion. In short, it’s lighter than aluminium, stronger than iron, and more corrosion-resistant than both." CFRP fabrication Raw strands of carbon fibers are heated to increase thermal conductivity.
The mixing of raw carbon fibers and compound resin is critical. Further heat treatment of the composite ensures greater strength. The strength ratio of the material is assessed to ensure rigidity and quality compliance.
The design of lightweight materials for the A350 structure is a complex and iterative process performed by Airbus and its collaborators. The CFRP process starts with controlled heat treatment of the raw fibers. Proper heat treatment of carbon nanofibers results in higher thermal conductivity and greater strength.
Individual threads are bundled together to form a fiber matrix, which is then hardened using resin. On the A350, high-quality composites with precisely shaped sheets of fibers are used to achieve the required level of rigidity. Similarly, the load-bearing properties of the CFRP are achieved through a precise fabrication process.
The Strength Ratio (SR) is the ratio of the maximum load that can be accepted by the composite and applied load. Comparing these two approaches to aircraft manufacturing. It is worth noting that manufacturing composite materials is energy-intensive and causes a higher environmental impact.
However, several studies have shown that composite structures contribute to a 15-20% reduction in environmental emissions over time. A lightweight structure Most of the A350’s wings are made up of such high-strength composites. The A350 wings are among the largest single structures made from carbon fiber composites.
Similarly, the fuselage, including the wingbox which connects the wings to the fuselage, is made of carbon-based composites. Get the latest aviation news straight to your inbox: Sign up for our newsletters today. As Airbus states, "The application of carbon-fibre reinforced plastic reached new proportions with the A350 XWB, which boasts a significant application of composites throughout.
For example, most of the A350 XWB's wing is comprised of the lightweight carbon composites, including its upper and lower covers." The extensive use of lightweight materials on the A350 directly contributes to its net fuel burn. A lighter structure can carry payloads further than a conventional aluminum structure.
During its operational life, the A350 requires less maintenance due to the overall strength of the airframe. Composite materials increase the life span of the aircraft. Moreover, the excellent corrosion resistance of the materials increases the lifetime of the airframe.
Airbus claims that the A350 XWB requires 50% fewer maintenance tasks, and the airframe checks clock in at 12 years compared to eight years on the A380 . Airbus manages the composite scrap by recycling it for various other uses. Thermoplastic CFRPs can be re-melted and reused in multiple ways, which Airbus and its suppliers take advantage of.
Using lightweight and robust composites reduces net fuel burn and minimizes maintenance costs..
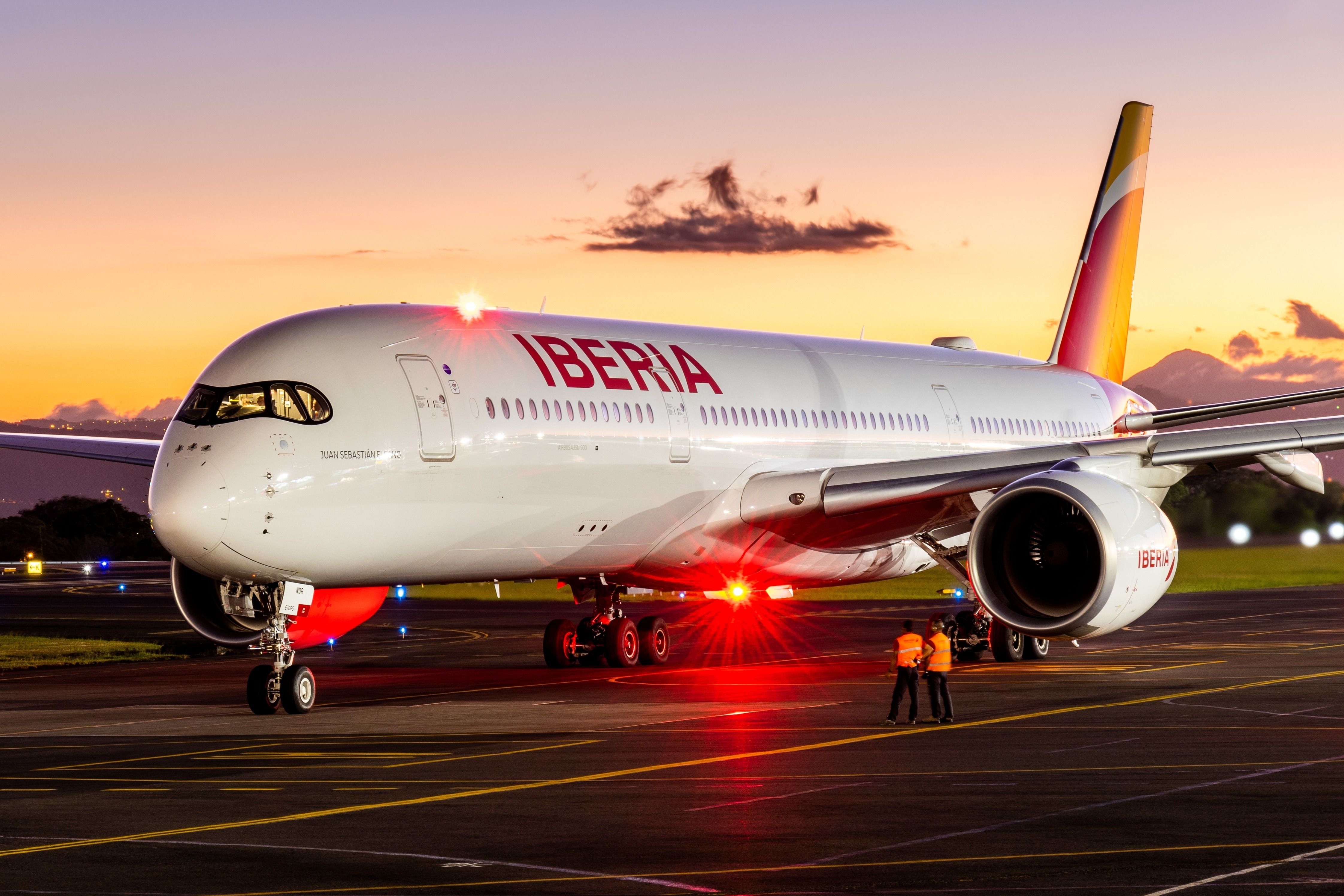