Summary Boeing publicly shared its Product Safety and Quality Plan after FAA criticism. Areas of focus include SMS, simplifying processes, and training enhancement. Intense Boeing-FAA engagement and oversight is in place to ensure plan execution.
The door plug blowout on the Alaska Airlines Boeing 737 MAX 9 flight in January became a highly publicized event and a deep embarrassment for Boeing . It led to the Federal Aviation Administration (FAA) issuing the second grounding for the Boeing 737 MAX since its initial introduction in 2017, while it ordered inspections of each door plug. Yet, worse was to come for Boeing.
After the National Transportation Safety Board (NTSB) issued preliminary findings that showed four bolts meant to hold the door plug in place were missing, the FAA auditors descended on the Boeing 737 assembly line. The subsequent FAA report was sharply critical of Boeing, citing "gaps in Boeing's safety journey," and in late February, FAA Administrator Mike Whitaker gave Boeing 90 days to come up with a plan to fix the problems. The Boeing roduct Safety and Quality Plan Boeing subsequently made public an 11-page summary of its Product Safety and Quality Plan , which describes the company's planned improvements in seven specific areas.
It also met with the FAA in May to review the plan, which Whitaker described as “a guide for a new way for Boeing to do business,” adding that he expects the company to produce “systemic change.” The FAA and Boeing now meet weekly on the progress of implementing the plan, and the FAA conducts monthly reviews. But what are the seven areas that Boeing is focusing on? Here’s what you need to know: 1.
Safety Management System (SMS) Boeing is in the process of developing an enterprise-wide SMS and has laid out plans to deepen its reach within the production system. Some key initiatives include: Employee reporting: The “Speak up” system for anonymous reporting of safety or quality issues by employees is being enhanced. This will include promoting the benefits and confidentiality protections, as well as advanced data analytics to expand risk analysis.
These efforts led to a 500% increase in submissions in Q1 2024 alone. Traveled work: Part of the issue with the Alaska Airlines aircraft is that it moved down the line before all work was completed at a station, and the door plug bolts were overlooked. Boeing is implementing a ‘move ready’ process that prohibits aircraft from moving to the next factory position until all milestones are completed.
Systems integration: In a nod to sub-par technology processes, Boeing plans to further integrate its safety and quality management system (QMS), with expanded reporting and analytics made available to management and regulators. 2. Simplification of processes and procedures Boeing is assessing the approximately 400 QMS command media to remove redundancies, eliminate contradictions, and create a simpler architecture.
Streamlining command media emphasizes creating more transparent and concise processes to help employees better understand their obligations, execute instructions, and overcome roadblocks. 3. Supply chain defect reduction Boeing is doubling down on supplier oversight and monitoring to ensure that parts from suppliers are conforming and compliant.
There are four main initiatives in this area: Data analytics: Strengthening data analytics capabilities to provide proactive notification of supplier issues, including the creation of an advanced analysis tool. Supplier oversight: Standardizing supplier oversight actions to prioritize safety and quality, including a standard supplier engagement model. Processes: Simplifying and improving supplier quality processes, including tightening acceptance criteria.
Industry engagement: Working with industry partners to drive change and dialogue about quality and safety issues. 4. Training Boeing has added over 300 hours of coursework to its foundational training curriculum for new mechanics and inspectors, as well as those who need or request additional training.
Further enhancements by late 2024 will see new manufacturing and quality employees receive up to two more weeks of foundational training, followed by enhanced structured on-the-job training (SOJT). 5. Production system compliance Boeing is reportedly making significant changes in this area based on the FAA's audits and findings.
It targets improvement in four critical areas of production system compliance: foreign object debris (FOD) control, tool control, parts and materials control, and employees’ adherence to work instructions. Boeing is also enhancing its daily reviews and audits in all four priority areas and throttled production activities upon discovering significant non-compliances. 6.
Engagement and communications Another key facet for Boeing is engaging and communicating with all employees to strengthen its culture of safety, quality, and compliance. It has been putting in place full-day quality stand-downs, creating and supporting employee involvement teams to conduct weekly problem-solving sessions and review employee ideas for production system improvement, and establishing a leadership program for quality and fulfillment managers. 7.
Installation plan improvements Installation Plan (IP) work instructions, which are used to translate often-complex engineering requirements, can be demanding for mechanics to understand. Boeing is implementing a plan to examine the design-build process for opportunities to enhance the safety of critical systems and structures, and simplify and clarify work instructions in IPs. The FAA reacts The FAA and Boeing met at the end of May for an extensive review session of the new business plan, and Whitaker seemed to signal that it was a productive first step in what is likely to be a lengthy process.
In a statement, the FAA shared: "Today, we reviewed Boeing's roadmap to set a new safety standard and underscored that they must follow through on corrective actions and effectively transform their safety culture. On the FAA's part, we will ensure they do and that their fixes are effective. This does not mark the end of our increased oversight of Boeing and its suppliers, but it sets a new standard of how Boeing does business.
” The planemaker still has a long way to go...
What happens next? Whitaker has emphasized that the FAA and Boeing will have “constant engagement” going forward, ranging from FAA inspectors on Boeing’s factory floor daily, to weekly senior meetings, and quarterly meetings between the CEO and FAA administrator. The FAA limited Boeing production of the 737 Max after the Alaska Airlines incident, and that cap will remain in place until the agency is satisfied Boeing is making progress. New Boeing CEO Kelly Ortberg has a long road ahead as he implements this seven-step safety program.
But he has already made a critical first decision: To be based in Seattle rather than the corporate headquarters in Virginia, saying: “Because what we do is complex, I firmly believe that we need to get closer to the production lines and development programs across the company. I plan to be based in Seattle to be close to the commercial airplane programs.” Time will tell whether he can restore Boeing to its former position at the pinnacle of global aviation engineering.
Kelly Ortberg began working as the chief executive of Boeing on August 8..
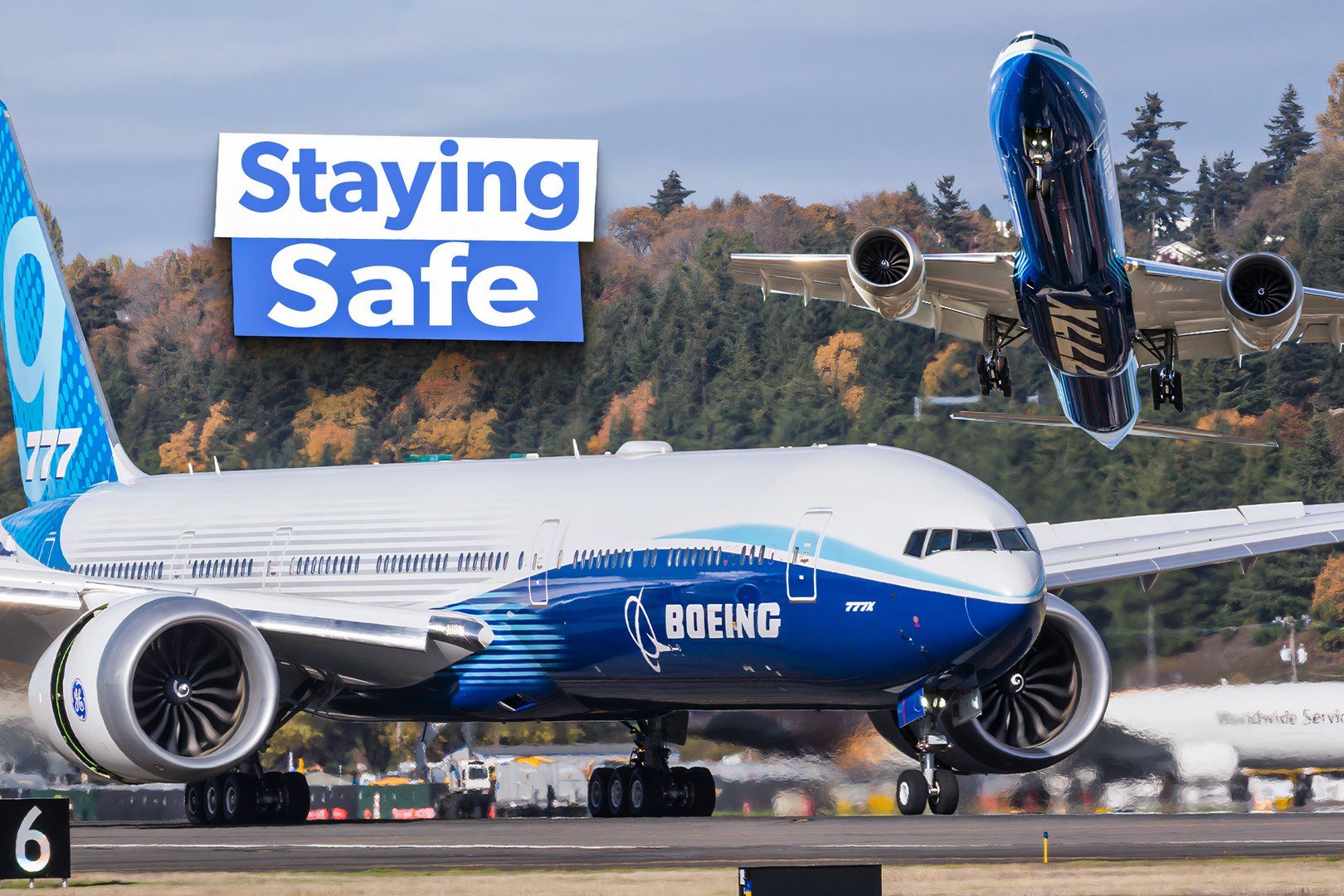