With such a significant presence in the state of Washington, many may know that the Boeing 737 , as well as many other well-known aircraft types, are born at the Renton Factory. Home to a large production facility, Boeing has been producing its best-selling single-aisle aircraft at the site for decades. In fact, the 737 family is known as the most-produced commercial aircraft in aviation history.
However, it would not be possible without 1.1 million square feet of factory space. Boeing touts its factory site as a leader in the industry when it comes to efficiently developing aircraft.
Since the 737 program began in 1967, more than 10,600 jets have been rolled out of the production facility. Just as the company has focused on innovation over the years, operations within the factory itself have evolved. Although the 737 MAX may look similar to its previous generation counterparts – the 737 Classic and the 737 Next-Generation (NG) – each generation has different features, which results in various practices and tests during assembly.
A little over a week With more workers and advanced technology, the final assembly of a 737 MAX takes about 10 days – one day less than the 11 it took for the 737 NG. However, the beginning of a 737 MAX’s life takes place nearly a thousand miles away in Kansas. Fuselages are developed by Spirit Aerosystems in Wichita, and then they are transported by freight train to Renton .
Once the fuselage arrives, Boeing will begin installing the necessary equipment and features. Between days one and three, the following are equipped on the fuselage: Insulation Hydraulic systems Electrical wiring On the exterior, assembly workers will install the dorsal fin, and if the airline requests the plane be equipped with WiFi, an antenna and protective radome will also be installed. Spirit AeroSystems will furlough hundreds of workers after suffering losses amid Boeing's 737 MAX slowdown.
It is not until day four that the fuselage begins to appear more like an aircraft. This is because the wings, including the horizontal stabilizers, are then placed on both sides. The tail and vertical stabilizer are also installed along with the landing gear on the bottom of the fuselage.
On day five, assembly workers will then bring in the rear galleys and lavatories. The aircraft is also equipped with water tanks and waste compartments, while cable riggings are connected to the flight control systems. The aircraft’s fuel tank also goes through a final pressure test during the fifth day of assembly.
Days six through 10 Once the process reaches the sixth day, Boeing introduces the aircraft to oil and power for the first time. This marks the beginning of necessary mechanical and electronic tests on the plane. Other elements inside the cabin are also installed, such as the sidewalls and overhead bins.
The forward galleys and lavatory are also placed inside on day 6. After a week of assembly in the factory, mechanics will begin testing the pressurization of the cabin. The aircraft’s fuel tank is also inspected thoroughly and cleaned.
Assembly workers will then begin tests on the plane’s flight control systems and landing gear to ensure it is working properly. The interior will begin to appear more like an aircraft on day eight, as Boeing will install the carpets and passenger seats. This process may take longer as each airline has different seating layouts and capacities.
For example, Alaska Airlines ’ 737 MAX 8 accommodates 159 passengers, while United Airlines 737 MAX 8s has 166 seats. Southwest Airlines' 737 MAX 8 can carry 175 passengers onboard, given that the plane is a single cabin. Alaska and United both have first class and premium sections of the main cabin with increased legroom.
Also, on day eight, flight control tests continue, including the aircraft’s hydraulic systems. A thorough quality inspection also takes place. The 737 MAX’s two engines are mounted on its wings on day nine.
Once installed, they are connected to the plane’s electronic and hydraulic systems. As Boeing prepares to roll out the aircraft from the production facility for the first time, assembly workers will conduct final inspections. This portion occurs before the full presentation to the customer.
Day 10 is reserved for any final installations that were pending or any tests or assessments that are required to be performed on the aircraft. Once it is officially rolled out, there are still several more days before it will welcome passengers onboard. After leaving the production facility, the plane will perform preflight testings and be painted in the customer’s livery before finally being delivered.
Working through the complications Boeing has an impressive three assembly lines for the 737 MAX at the Renton factory. Last year, The Seattle Times reported that a fourth line would open this year, replacing a 787 Dreamliner assembly line. However, recent complications surrounding the company spawned by the Alaska Airlines 737 MAX 9 door blowout incident earlier this year appeared to have delayed Boeing’s ambitions.
On August 7th, the Federal Aviation Administration (FAA) said it is continuing to hold Boeing accountable after the door blowout incident. The agency has an aggressive oversight of the company to ensure it fixes its systemic production quality issues. Since Boeing’s complications, its rate of 737 MAX production has slowed, prompting airlines to suffer from increased delivery delays.
According to Inc. , the FAA capped Boeing’s production of the aircraft to 38 planes per month, which is below its projected production of 45 aircraft every month. The move halts Boeing from achieving its July 2025 goal of producing 57 planes per month.
Simple Flying previously reported that the planemaker warned its customers that delays could extend through 2026. The aircraft type’s other two variants – the MAX 7 and MAX 10 – are still yet to be certified. Despite being an Airbus customer with a fleet of pre-owned airframes, the carrier surprisingly opted for the 737 MAX instead of the neo.
.
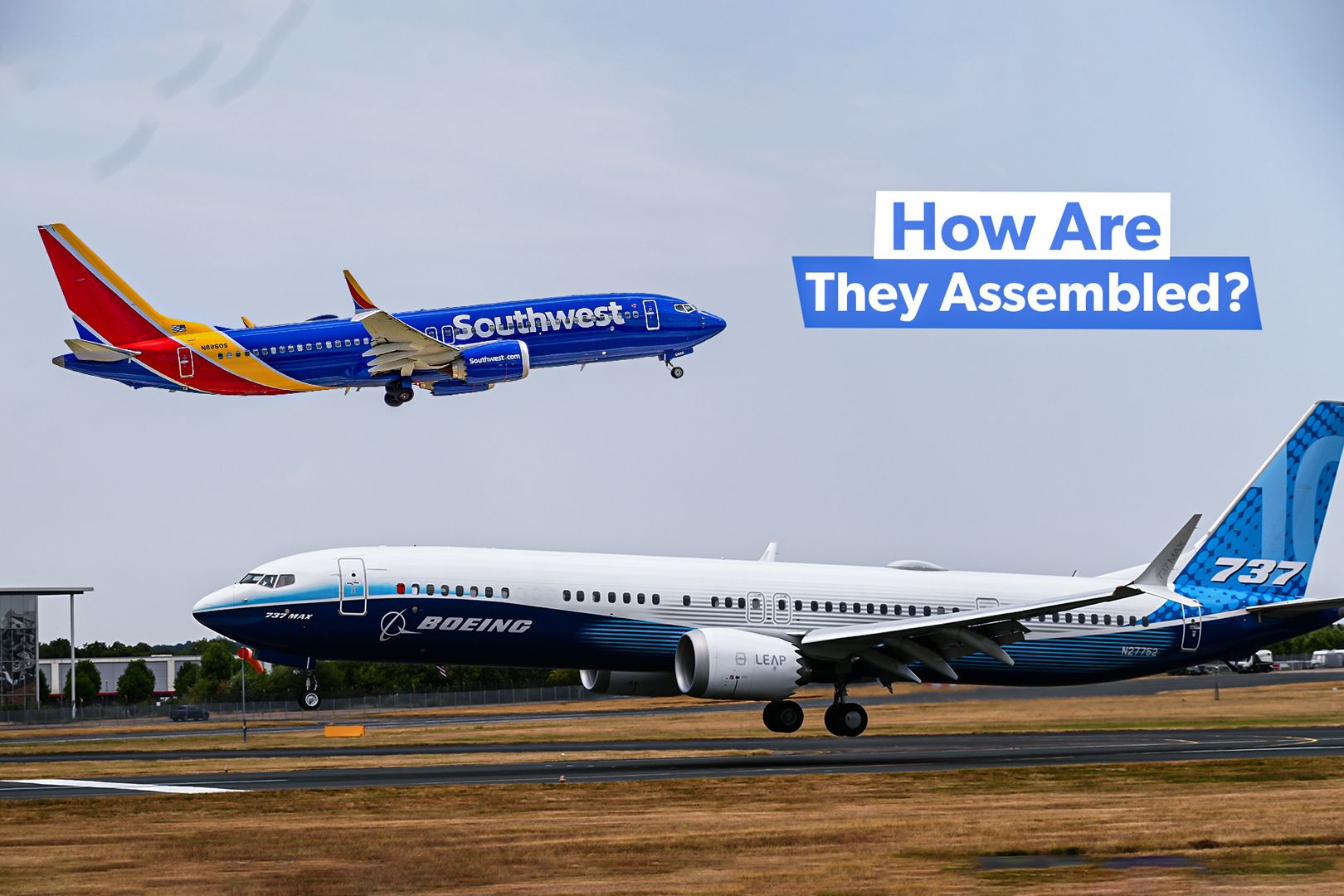